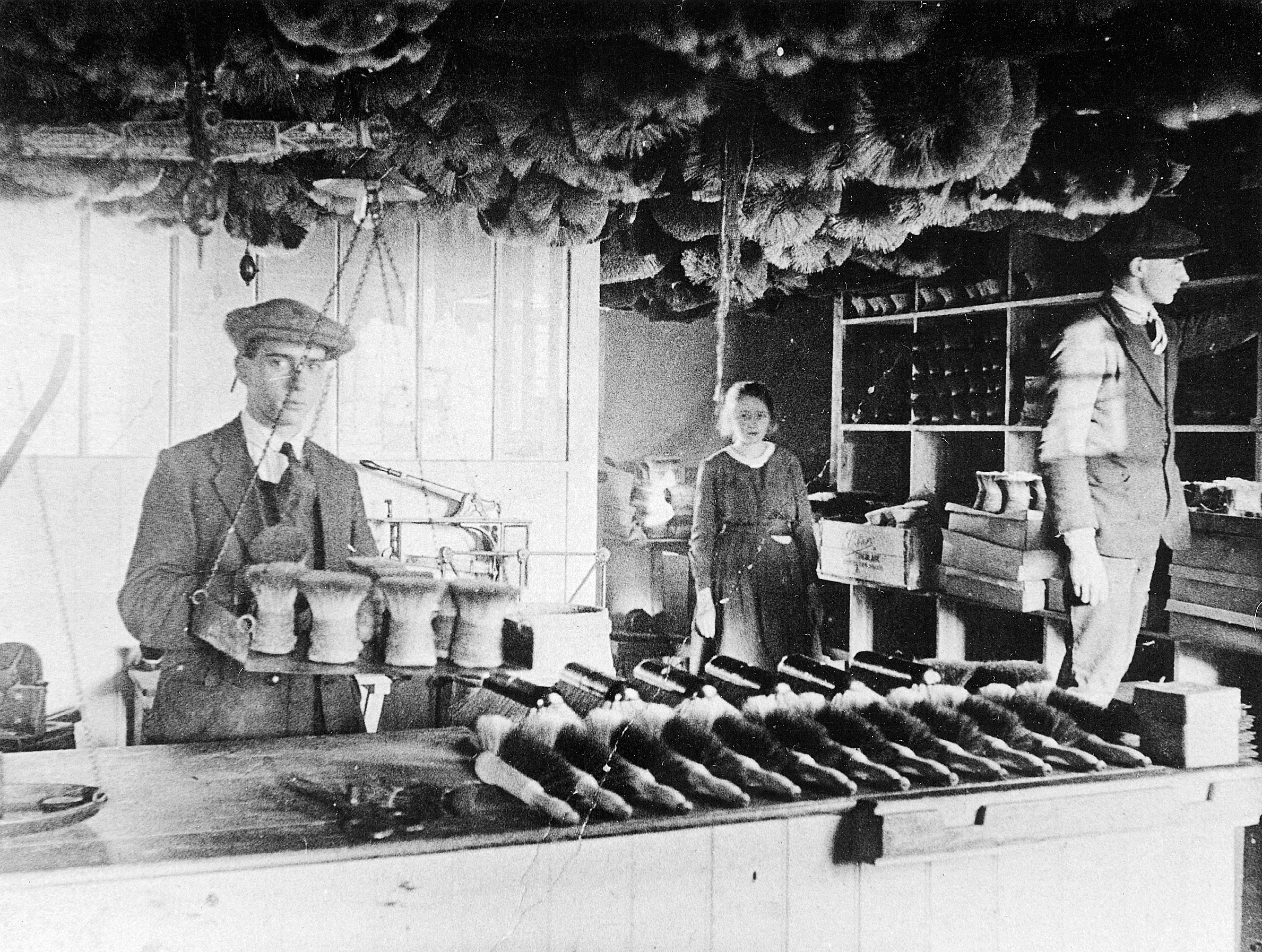
The Broad family in brush making
Biography of Alex Broad
W.L.Broad, “Lawson”, followed his father into the Brush Trade. Alfred Carter Broad, “AC”, born 1851 in Diss, Norfolk, apprenticed into brushmaking, in London. After meeting and marring in 1876, Martha, nee Osbourn, of Eye, they set up home above his fathers hard ware shop in Bury St Edmunds, making brushware for local farmers.
Not finding enough scope, he decided to emigrate, with his wife and two daughters. Sailing on 29th Dec 1879, on the powder ship “Coromandel”, on lease to the NZ Shipping Co, with 31 passengers and a cargo of 400 tons, including 25 tons of gunpowder, arriving at Dunedin, NZ, on 31st March 1880, after a voyage of 105 days. He then established and built up the Otargo Brush Company, had 4 more daughters before “Wilfred Lawson” arrived in April 1890, the 7th child.
“AC” built a larger factory, and as soon as “Lawson” was old enough, joined the firm and went on to become a very expert engineer. As a very wilful young man, with a liking for beer and his father being a very strict Presbyterian, they soon fell out. After his marriage to Dorothy a son was born. So it was up sticks and set sail to England, arriving in 1932. Touring around the country in a caravan, with a wife and child, visiting different Brush Makers, they eventually arrived in Chesham.
“Lawson” fell in love with the “Chilterns”, and that is where he settled, joining the firm of Webb and Foulger, later to become Webb, Jarrett and Co. Ltd. as Chief Engineer. Webbs at that time was still rather a backward company, mostly candlelight for the women pitch pan setters and wire drawer hands, with a big steam engine to power the machinery, cutting out brush backs, from beech logs delivered from local woods by horse-drawn timber wagons.
The first thing” Lawson” put in was electricity for lighting and power. He then set about designing and building a bass broom-making machine. He proved himself a very capable engineer by correcting a heavy power belt that kept breaking, by the simple expedient of putting a twist in the lower belt of 360 degrees so that the join would go over the central pulley.
“Lawson” then went on to design a pair of wood mill “shaping machines” which were twin-headed, with horizontal cutters, with built in electric motors, and automatic safety guards. His next project was to re-design and build two “gents military hair brush”-making machines from an original German machine, with the help of hired draughtsmen, the machines and drawings being rather complex.

Alex, his son, born April 1933, joined the firm in 1953, after completing his “National Service” in the “Oxford & Bucks Light Infantry”. Initially to go on the road as a salesman, but after several days out with established “Reps”, found that he was of a far more practical mind, so chose to stay in the factory, learning about the trade, its materials and processes.
A great teacher and guide was found in Pill Clements, the paint-brush Foreman, who spoke of the old brush makers in London, who always wore top hats, so were known as “gentlemen brush makers“. Also Denis Powel, the bristle dresser. His knowledge of pigs’ bristles from around the world was phenomenal. He even related a story of how Russian bristle used to be shipped to London, loose in wooden barrels, in a filthy condition and needed to be cleaned and sorted. On one occasion a barrel of loose bristle even included a severed human finger!
The bristle trade with Russia came to an end after the Russian revolution. Not being satisfied with killing the Tsars, they killed off all the Royal pig breeding stock as well! Good quality bristles were also used by tailors, for stiffening the lapels on gents’ jackets, and also by cobblers, to sew on the soles of shoes. These were known as “Dowry Bristles“, and were very highly valued. It was also said that if employees didn’t go to church on Sunday, they didn’t have a job on Monday.
Alex.Broad was appointed to the Paint-brush department, whose production averaged about 9 dozen brushes a week, with a staff of about 18. Production and staff gradually increased, and in its heyday, employing about 40 workers, it topped 100 gross in a single week.
Alex, by this time, after going on various courses, was asked to inspect a new paint-brush making machine in Nuremberg, Germany, which the firm later decided to purchase. This was a compressed-air operated machine and further increased output. At about this time “Lawson” began designing his own paintbrush making machine, even continuing after his retirement, but to no avail – he died in1976, at the age of 86, with the machine unfinished.
After the Russian revolution in 1917, most of the bristle was imported from China, with small amounts from Poland, Korea, Manchuria and India. The Americans had imposed a strict trade embargo on China at the start of the Korean War, but had large strategic stockpiles, which it released parcels of from time to time, upsetting the world market.
At about this time a rival firm in Chesham sent one of its directors to China, to teach them how to make paint brushes. Within a few years they were asked to sell quite good, if only of the DIY quality, nicely carded for display in the shops, priced at less than the cost of the bristle. China needed Stirling, as they were wanting to buy Harrier Jets.
The writing was on the wall! It was soon after this that the firm did a big marketing drive, which was soon withdrawn though lack of sales, that the firm decided to sell the Chesham site to a DIY Shop Chain, and relocate some of the machines to Chepstow, in South Wales.
The paintbrush machinery etc. was sold off to a firm in South Africa. The man who came to supervise the dismantling and shipping, was originally from Liverpool, but had very little regard for the welfare of the people who were to use the machinery in South Africa, saying, that if someone lost a hand or an arm, they could very easily be replaced, so did not require any guards or safety measures.
One of the big arguments that I had with the management, was to do with the amount of stock of materials that we carried, taking into account the time for replacements to arrive, as we needed quite a large and varied stock in order to satisfy customer requirements, without long delays, as we had quite a large regular and “special” order-book.
The main suppliers were “Stephens,” of Lowestoft for ferules, who employed women, who also worked at fish cleaning, when the North Sea trawler fleet used to land their catch, which was very seasonal. Many handles came from Tomlin and Smith, of Chippenham, again a very seasonal business, as they made turned handles from coppiced trees, which had to be cut and seasoned before turning.
The order book included Ministry of Defence contracts, which included rifle cleaning brushes and general purpose brushes, “if it’s fixed, paint it, if it moves, salute it” which were occasional, but good bread and butter business. We also did “special” glue brushes for the “British Museum” book binding department, with special ferrules, handles and “bridles”.
The range of brushes we made was quite extensive, as we had built up a very good base of experience, techniques, and equipment, so we could do practically anything! One of the strangest requests was for small round surgical brushes that were intended for use in brain surgery, made with special fibreglass filaments. The idea being that after drilling a hole into someone’s skull, this brush would be used to clean up the drillings. However, it was found that bits of fibreglass broke off !